The rapidly evolving, interconnected industrial landscape demands that companies make informed decisions about their strengths, limitations, and growth potential. One powerful way to do that is through industry capacity mapping—a process that offers deep insights into the availability, functionality, and readiness of resources, infrastructure, and production capabilities across entire sectors.
The ability to visualize and evaluate capacity across a supply chain is becoming increasingly critical to ensure operational efficiency and to support strategic planning, competitive positioning, and crisis response.
From mitigating risks to scaling up for growth, capacity mapping is the compass that modern industries can’t afford to ignore.
What is industry capacity mapping?
Industry capacity mapping is the systematic evaluation of an industry’s ability to produce goods and services. It includes the analysis of current production capabilities, available resources, infrastructure, workforce capacity, and future growth potential. At its core, it serves as a blueprint that reveals where strengths, gaps, and bottlenecks exist within an industry.
This process goes beyond simple data collection—it integrates manufacturing capabilities assessment, workforce and resource allocation, and industrial infrastructure analysis to provide a comprehensive overview of production realities. In turn, this empowers companies, governments, and industry leaders to align strategies with actual capabilities and market demands.
Why Is Industry Capacity Mapping Gaining Importance Today?
As global disruptions and shifting market demands continue to challenge industries, industry capacity mapping has become more crucial than ever. It helps businesses gain supply chain visibility, identify gaps in production capacity planning, and uncover potential bottlenecks in resources and infrastructure.
With the rise of digital tools, data analytics, and a growing focus on sustainability, real-time insights have become essential for maintaining operational efficiency. Capacity mapping enables businesses to transition from reactive strategies to more proactive, informed decision-making, making sure they remain competitive and resilient.
How does industry capacity mapping support strategic decision-making?
Industry capacity mapping serves as a foundational element in strategic planning, supporting efforts in areas like:
Investment Prioritization
Capacity mapping helps businesses pinpoint high-potential areas where investments in infrastructure or automation will yield the greatest return. This allows companies to focus resources on projects that offer the most value and efficiency improvements.
Market Expansion
By understanding regional capacity, businesses can make informed decisions about where to expand or scale back operations. This insight ensures that resources are allocated effectively to meet demand in new or existing markets.
Risk Management
Capacity mapping highlights vulnerabilities and dependencies within the supply chain, helping businesses anticipate potential disruptions. By identifying these weak points, companies can implement strategies to mitigate risk and maintain operations during crises.
Innovation Enablement
Accurate capacity mapping ensures that innovation efforts align with available manufacturing or technological capabilities. This allows companies to invest in new products or services without overextending their resources or compromising quality.
What sectors benefit most from capacity mapping?
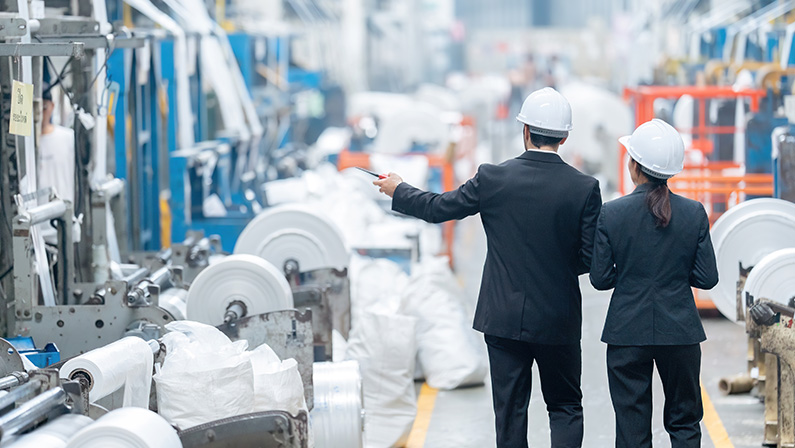
While nearly every industry can gain value from capacity mapping, certain sectors stand to benefit the most due to their complexity and reliance on interdependent systems.
Manufacturing
Capacity mapping identifies gaps in manufacturing capabilities, helping businesses pinpoint areas for improvement. This insight is crucial for enhancing production efficiency and meeting growing demand across industries like automotive and electronics.
Healthcare and Pharmaceuticals
Capacity mapping is vital in ensuring timely access to medications and medical devices, especially in times of increased demand. It helps optimize resource allocation and manufacturing processes, ensuring critical supplies are available when needed most.
Energy and Utilities
For the energy sector, capacity mapping supports the planning of increased demand and the transition to renewable energy sources. It allows companies to balance supply and demand while investing in infrastructure for sustainable energy solutions.
Defense and Aerospace
In defense and aerospace, capacity mapping is critical for maintaining national readiness and ensuring production agility. It helps optimize resources, reduce lead times, and meet the demands of defense contracts and aerospace innovations.
Logistics and Transportation
Capacity mapping enhances supply chain visibility and improves route optimization. By understanding transportation capabilities, businesses can streamline operations and reduce costs, ensuring faster delivery and better service.
How is capacity mapping conducted in practice?
The process of conducting industry capacity mapping involves several key steps:
- Data Collection: Gather data on existing production facilities, machinery, workforce, and throughput capacity.
- Resource Evaluation: Assess workforce and resource allocation, including labor skill levels and availability.
- Infrastructure Review: Conduct an industrial infrastructure analysis to evaluate the quality and accessibility of supporting facilities.
- Scenario Modeling: Use simulation tools to model different market or production scenarios.
- Visualization and Reporting: Create dashboards or reports to share findings with decision-makers.
What are the key metrics used in industry capacity mapping?
Understanding the right metrics is crucial to effective capacity mapping.
Here are some of the most impactful ones:
- Production Throughput: Measures how much product can be made in a given timeframe.
- Equipment Utilization Rates: Assess how much of the available machinery is actively used.
- Labor Productivity: Evaluates output per worker or per labor hour.
- Downtime and Bottleneck Rates: Tracks delays in production and identifies recurring issues.
- Inventory Turnover: Measures how often inventory is used and replaced, critical for production capacity planning.
- Lead Times: Time taken from order placement to fulfillment—important for supply chain visibility.
How can businesses use capacity mapping to enhance competitiveness?
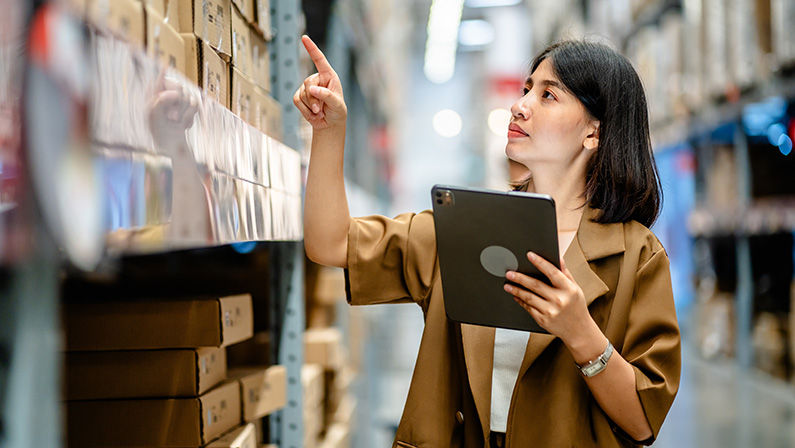
Capacity mapping is not just about identifying current capabilities—it’s about building future advantages.
Benchmarking Performance
By comparing capacity metrics with industry standards, businesses can pinpoint areas where they may be falling short. This provides valuable insights for setting performance goals and improving efficiency.
Identifying Untapped Potential
Capacity mapping uncovers underutilized assets and capabilities that can be scaled to meet growing demand. By recognizing these opportunities, businesses can optimize operations and increase output without significant investment.
Improved Forecasting
With a clear understanding of production capabilities, businesses can align output with market demand more accurately. This leads to better inventory management and a reduction in overproduction or stockouts.
Resource Optimization
Capacity mapping ensures that workforce and resource allocation are aligned with both business priorities and market needs. This results in more efficient operations and a better return on investment.
Customer Satisfaction
Efficient capacity management leads to faster, more reliable production, reducing lead times. As a result, customers receive products on time, boosting satisfaction and fostering loyalty.
What role does capacity mapping play in crisis response and recovery?
Capacity mapping is essential during crises, offering real-time insights into a business’s resources, production capacity, and workforce allocation. This helps companies make quick, informed decisions, prioritize critical processes, and address bottlenecks. Post-crisis, capacity mapping enables businesses to assess recovery progress and adapt strategies, ensuring better resilience and a smoother recovery for future disruptions.
What are the challenges in implementing effective capacity mapping?
Despite its value, industry capacity mapping isn’t without hurdles:
Data Gaps and Inconsistencies
Incomplete or outdated data can distort the accuracy of capacity mapping, leading to flawed decision-making. This can result in inefficiencies and missed opportunities for optimization.
Integration Issues
Coordinating capacity mapping across various departments and platforms can be challenging. Lack of seamless integration may cause delays and hinder the effectiveness of the mapping process.
Scalability Concerns
For large or multi-national operations, capacity mapping requires scalable digital infrastructure. Without this, businesses may struggle to manage complex, global supply chains effectively.
Cost and Time Investment
The initial implementation of capacity mapping can be resource-intensive. Businesses must invest significant time and capital to set up systems and ensure data accuracy across all relevant areas.
What is the future of industry capacity mapping in a data-driven economy?
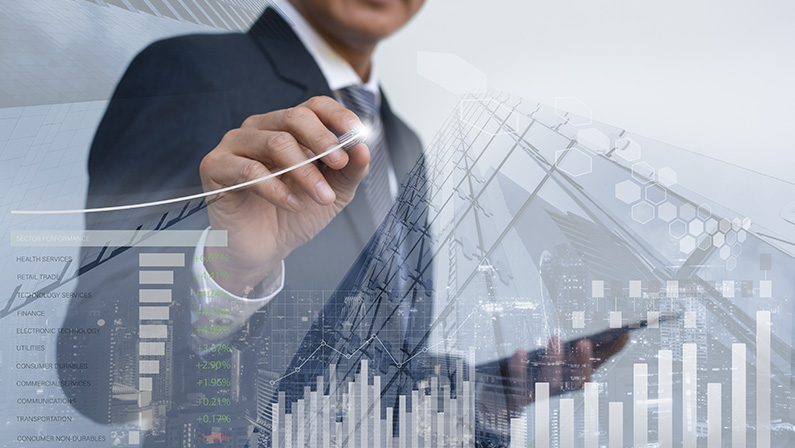
As industries adopt digital tools, the future of industry capacity mapping will rely on data analytics and AI. Real-time data and predictive modeling will optimize production capacity planning and resource allocation, helping businesses identify inefficiencies quickly. As automation advances, capacity mapping will become more precise, enabling proactive responses to market changes. Companies investing in these technologies will be better positioned to innovate, reduce costs, and maintain a competitive edge.
Driving Success Through Strategic Capacity Mapping
As global markets become more dynamic, understanding production capabilities is essential. Industry capacity mapping provides the clarity needed to drive growth, navigate disruptions, and stay competitive.
For businesses looking to optimize their planning, supply chain management consulting services from LSI offer a strategic advantage. With decades of experience, we improve manufacturing capabilities assessment, workforce and resource allocation, and industrial infrastructure analysis, streamlining supply chain processes from procurement to delivery for maximum efficiency. Contact LSI today!